Using cutting-edge technology to create the ‘Rain of Light’
The dome’s ‘Rain of Light’ effect is one of the defining features of the Louvre Abu Dhabi. It’s perfectly radiating geometry has been the subject of many models and mock ups over the years. Almost 8,000 metal stars overlap to form the geometric pattern of the dome. The pattern is repeated at various sizes and angles in the eight superimposed layers. Each ray of light penetrates the eight layers before appearing or disappearing as the sun’s path progresses throughout the day. At night, it forms 7,850 stars visible from both inside and out.
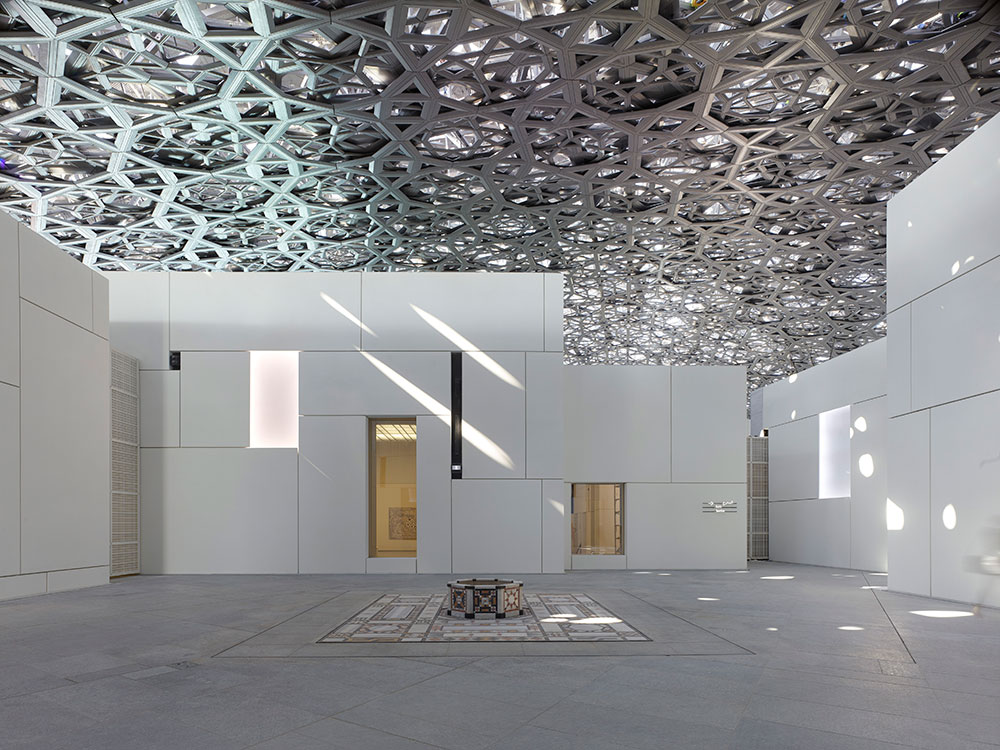
The complex structure of the domed roof of the Louvre, Abu Dhabi creating the “Rain of Light” in the exhibition space of the Ottoman mosaic pavement.
© Photography by Roland Halbe . Architecture by Jean Nouvel. Engineering by BuroHappold. Steel construction Waagner Biro.
To achieve this carefully contrived evanescent effect, the engineers from BuroHappold worked side by side with Atelier Jean Nouvel (AJN) for over a year. “We explored so many different solutions” explains Andy Pottinger the lead engineer: “Orthogonal geometries, stiff ring structures and geodesic approaches, but finally tried stripping the whole thing down to the architect’s base pattern. Suddenly we were working with the architecture, rather than just supporting it”. Instead of adding long straight lines they decided to create clusters of star-like shapes made up of squares and triangles. This pattern is repeated on each of the eight layers of cladding. From a geometrically logical pattern each layer was then scaled and rotated respectively to add further complexity and create the random effect of the ‘rain of light’.
Carefully contrived light levels
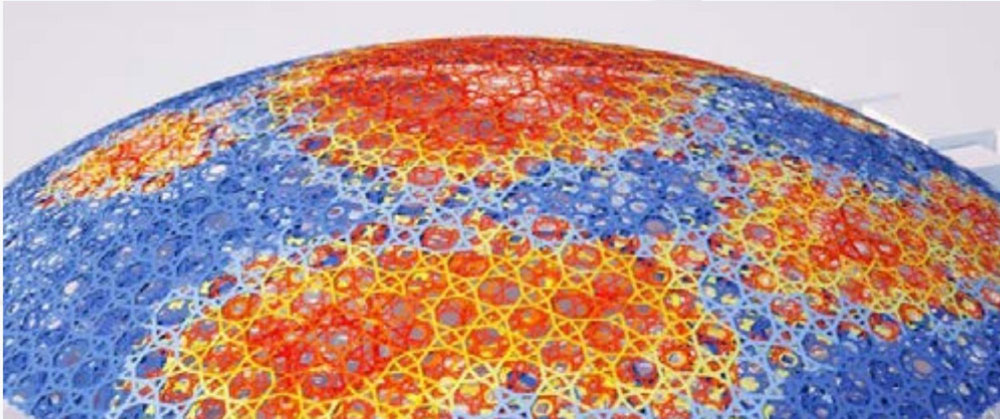
To control the level of light going through the dome light analysis mock-ups were used. The Louvre, Abu Dhabi. Architecture by Jean Nouvel. Engineering by BuroHappold
A series of light analysis models were provided by AJN showing the levels of brightness required in different parts of the building. Basing themselves on these indications the engineers developed a design tool to vary automatically the widths of the cladding system so as to obtain the required level of transparency. This involved extensively detailed design work if one considers that all eight layers put together make up an area of approximately 200,000 square meters. The structure of the dome structure was also designed to be self-standing thus avoiding the necessity of providing lateral steel barriers while the triangulated rim structure prevents the dome from spreading. To ensure that the bearing load was evenly distributed on each of the four massive concrete pillars, the dome is actually symmetrically placed along one axis.
A titanic construction site
Erecting and assembling a dome of this size, weight and complexity was a massive undertaking which Waagner Biro, the Austrian steel construction specialists pulled off remarkably. Using a 1,600- tonne crawler crane the workers hoisted 85 “super-sized” pre-assembled components weighing up to 65 tons. They were lifted from the nearby pre-assembly area to a specially designed temporary structure made up of 120 temporary towers. Each tower was different due to the irregular shape of the spaces below. Once assembly was completed, the entire dome was lifted by synchronized hydraulic jacks over 600 millimetres vertically to sit on their four permanent bearings.
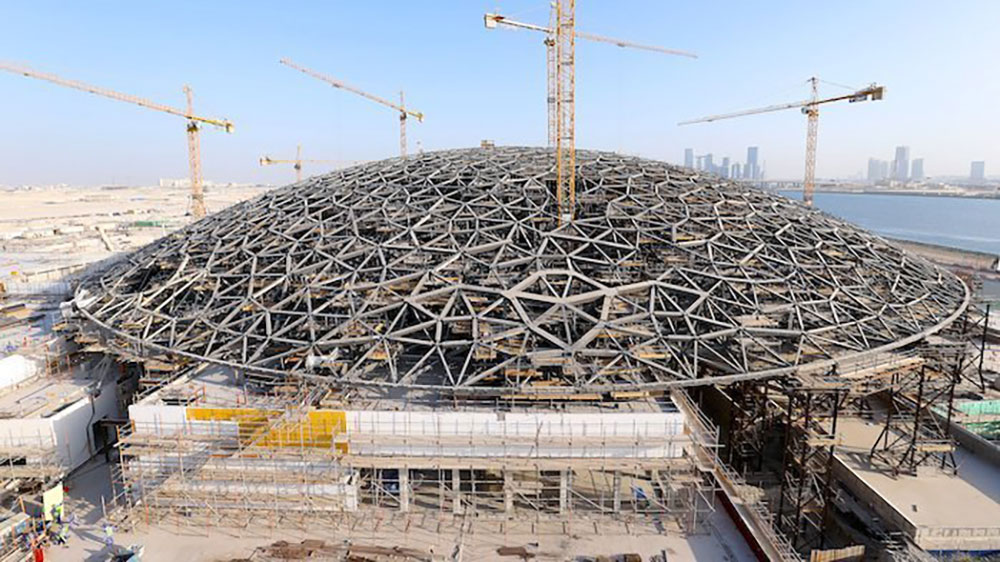
The dome of the Louvre, Abu Dhabi under construction.
Architecture by Jean Nouvel. Engineering by BuroHappold. Steel construction Waagner Biro.
A digitized data workflow
The whole structure is made up 500,000 individual parts, 10,968 steel elements and 2,796 connectors. A total of 5,200 tonnes of steel and 2,000 tonnes of aluminium cladding were installed. The handling of such a vast number of individual parts, both in the steel construction and in the cladding, was a particular challenge. A digitized data workflow was developed which included both the conceptual design, the manufacturing of individual components, the tracking of deliveries and on-site assembly and the clearance process of each component. Little wonder therefore if Waagner-Biro subsequently won the European Steel Building Award in September 2017.
Project information
Client: Tourism Development & Investment Company (TDIC).
Architect: Ateliers Jean Nouvel (AJN); Hala Wardé (HW architecture), partner architect; Engineering: Arup (sketches); BuroHappold
Gross floor area: 97 000 m2
Contractors: Joint venture Arabtec Construction LLC/San Jose SA/Oger Abu Dhabi LLC