Brass and brass PVD furniture: the use of brass by designers from the 1980s to the creation of contemporary furniture.
Brass in the 1980s was wildly popular, being used not just for furniture but also for cutlery and jewellery and has for some years now once again been making a firm come-back. This time around however there are subtle differences such as the use of square tube for furniture legs and frames instead of the round tube so ubiquitous in the eighties. If you look at the table base below left you will see a contemporary design that incorporates curves reminiscent of the 1950s along with the square-edge detail of today.
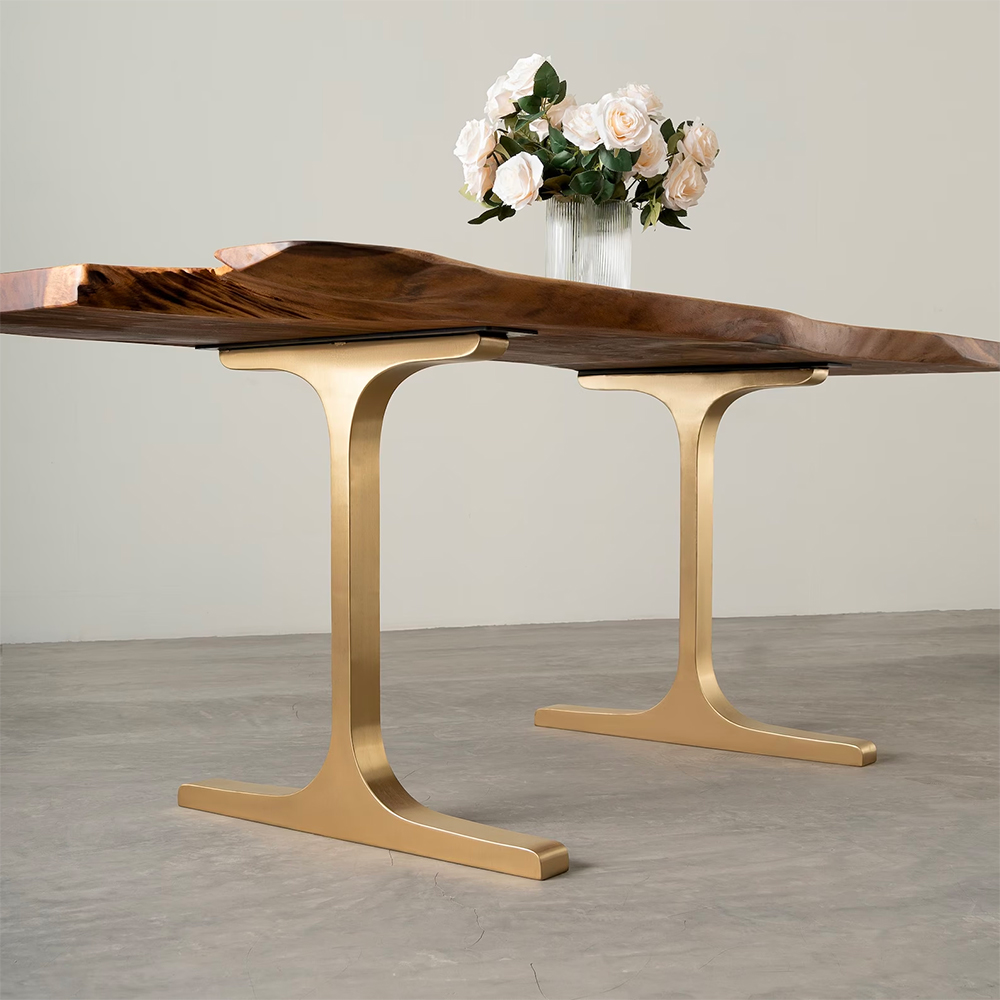
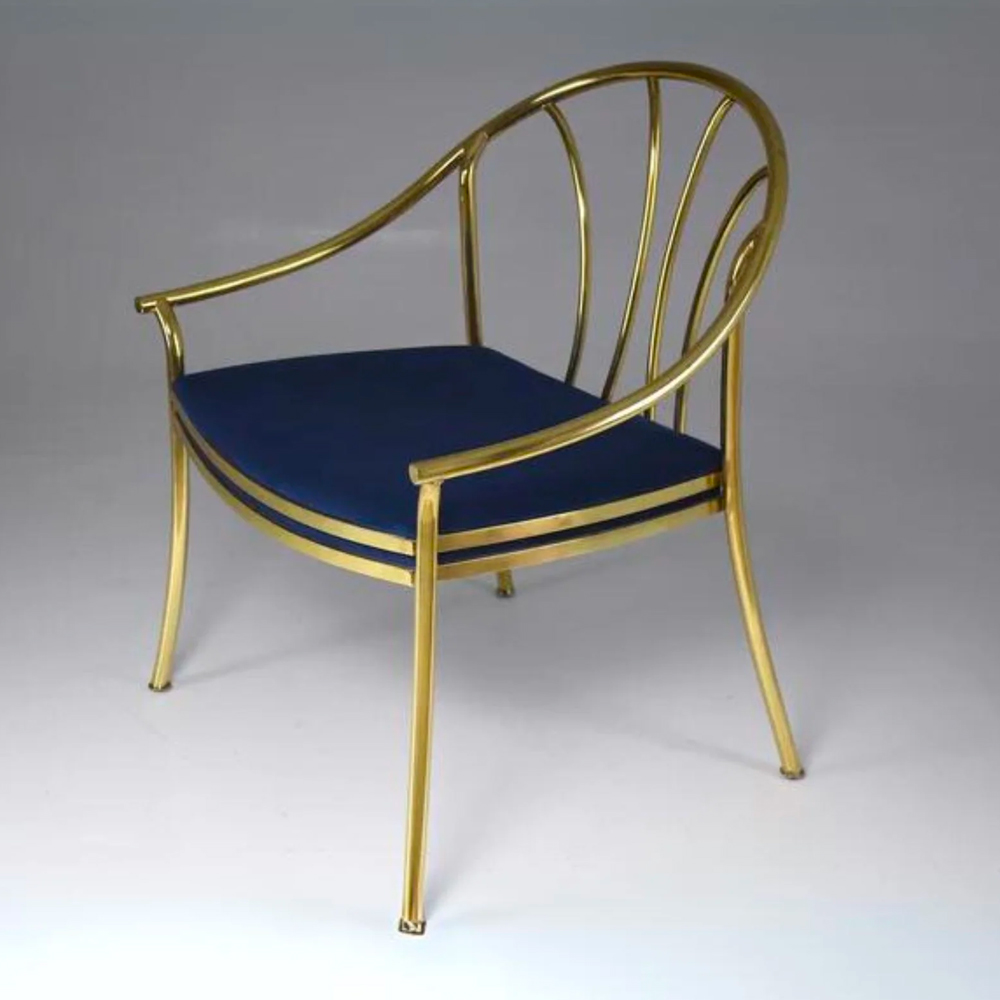
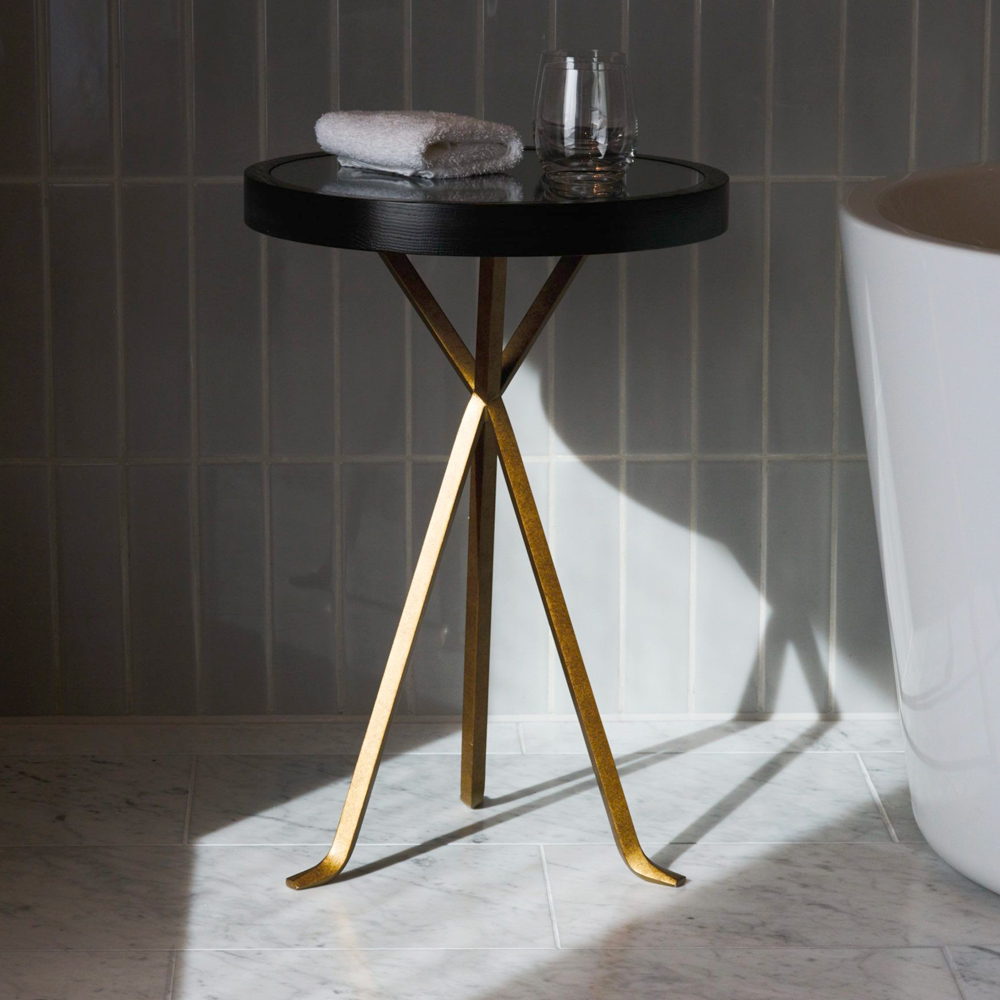
The central image shows a very typical 1980s design with almost all of the brass being circular tube. Brass in the 1980s was often lacquered, there being a horror of patina at that time however lacquer not only wears off but does so unevenly. So, with this furniture, there was always an uncomfortable feeling that the lacquer would need to be stripped and re-applied at a future date. Conversely, today, the patina that develops on brass is valued and admired.
In the right-hand image you can see a contemporary side table with square-edge flattened bar legs. This side-table base is fabricated from Brass PVD coloured stainless steel – as you can see it is used in a bathroom setting and has the the advantage of not tarnishing or developing verdigris as a result of being exposed to oxygen and moisture.
Brass and Brass PVD for hotel and casino shopfitting and furniture
Chrome had a resurgence over brass after the 1980s and enjoyed a few decades of popularity in offices and commercial environments but the gleam of brass has once again gained a foothold in hospitality interiors. The look now however is not of a cosy Old Worlde style nor of the over-reliance of round tube of the 1980s but has its own sleek and contemporary lines.
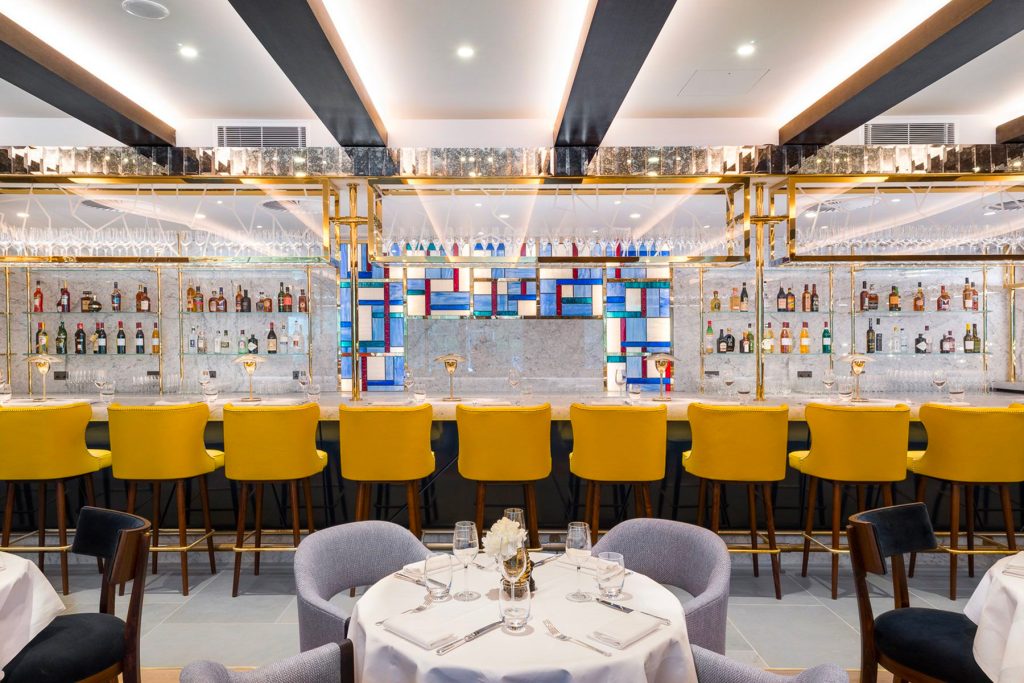
The Brasserie bar in the Devonshire Club Hotel with overhead glass rack in brass PVD coloured stainless steel.
The Devonshire Club Hotel, Interior Design: March & White, PVD coloured stainless steel: John Desmond Ltd
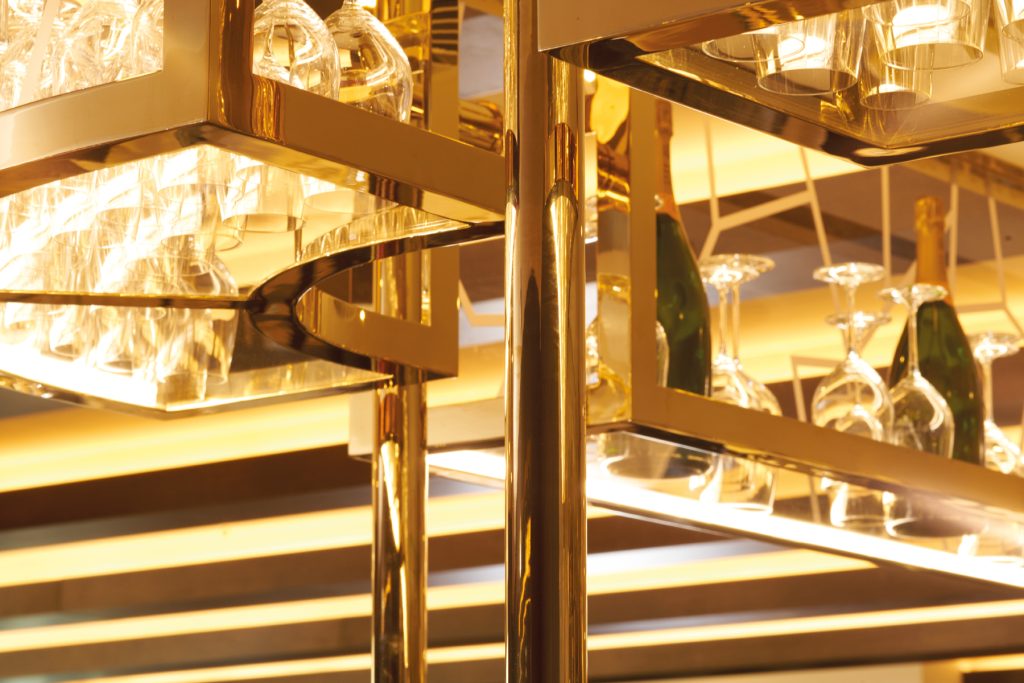
A close-up of the bar metalwork in Champagne Mirror PVD which has the look of a brass finish. The glass rack design combines rectilinear edges with curved profiles and large circular tube for uprights.
The Devonshire Club Hotel, Interior Design: March & White, PVD coloured stainless steel: John Desmond Ltd
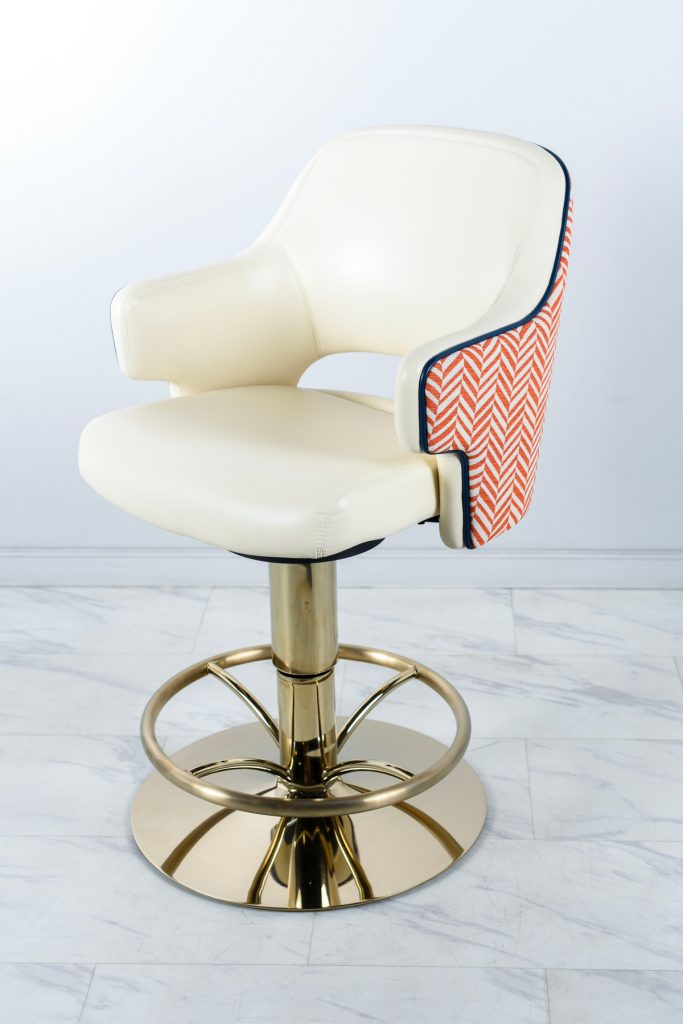
Casino chair by Gary Platt with base in PVD coloured stainless steel in Almond Gold which gives the look of a creamy brass colour. Chair base fabricated and coloured by Double Stone Steel Ltd.
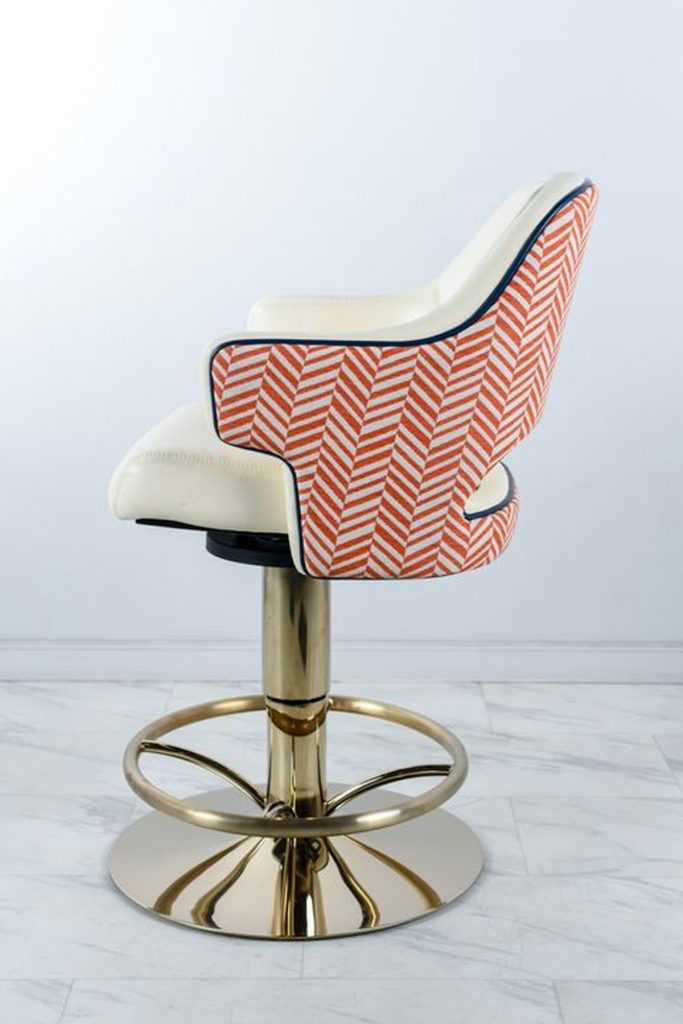
Casino chair by Gary Platt with base in PVD coloured stainless steel in Almond Gold which gives the look of a creamy brass colour. Chair base fabricated and coloured by Double Stone Steel Ltd.
Furniture for casino environments has to look – expensive! It also however has to be durable and stay looking good even with drinks spilled on it and rough use delivered by an all-night clientele. So the design of the fittings and furniture is carefully considered.
Clearly to make this casino chair from solid brass would be costly and create a very heavy chair. Stainless steel is 7% lighter in weight than brass. The mirror finish is not created by the PVD but is in fact the finish on the stainless steel itself, PVD is remarkable for allowing the substrate to – literally – shine through.
This manufacturer, Gary Platt, chose PVD stainless steel as a less costly material than brass but achieving the same warm, high-shine effect with the ongoing maintenance cost-saving of being able to wipe clean with a damp cloth by the everyday cleaning team.
If brass were used it would tarnish and need polishing and even if sealed would require (after wearing off unevenly) stripping and re-lacquering meaning removing the chairs from use whilst this is carried out. Using PVD avoids the inconvenience and expense as it does not tarnish.
Achieving a brass look for architectural applications, such as ceilings and cladding, with anodised aluminium
The colour of brass can also be achieved through the process of anodising although the process of colouring aluminium is very different to that of colouring stainless steel.
With the PVD process the stainless steel component or sheet is placed in a chamber with a titanium target and by heating the chamber to set temperatures the ions from the titanium coat the stainless steel to achieve a range of different colours. Cleaning the stainless steel prior to it going into the chamber is crucially important to ensure a high quality finish. Any marks or residue on the surface of the stainless steel will result in flaws and discoloration of the PVD finish. Despite the cleaning being so crucial its process is very simple, albeit thorough. It is carried out using citric acid and cloths so does not produce any waste chemicals, in fact the water residue drains away through the mains drains and does not require any specialist removal or treatment.
With aluminium the sheet or components is placed in a bath containing acid electrolytes, typically sulphuric or chromic acid, and an electrical current is passed through it forming oxygen on the surface of the aluminium and creating an anodic layer.
The natural colour is silver but, through the anodising process, the surface of the aluminium becomes porous and can absorb colourings which are added to create different hues.
The effect of gold anodised aluminium can be very striking in architectural as seen in the London Underground ticket hall ceiling shown above. Aluminium lends itself to ceiling applications being 69% lighter in weight than brass and around 66% lighter than stainless steel.
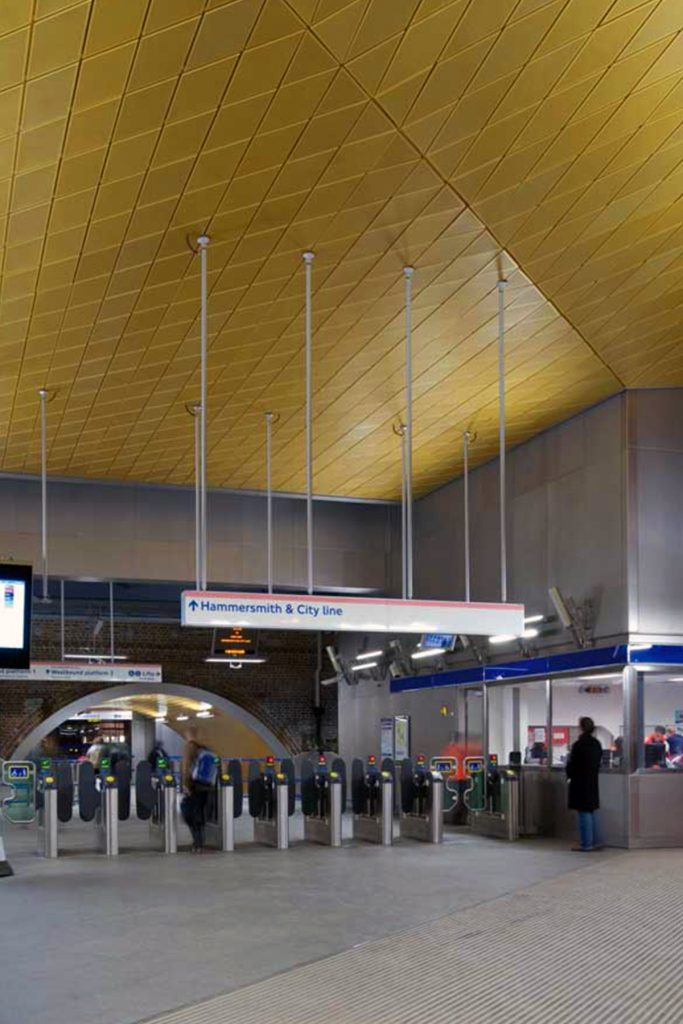
Showing the gold, or brass-coloured, anodised aluminium diagonally-set ceiling panels to the Wood Lane Underground Station, London. Architectural design by Ian Ritchie Architects. Ceiling by John Desmond Ltd.
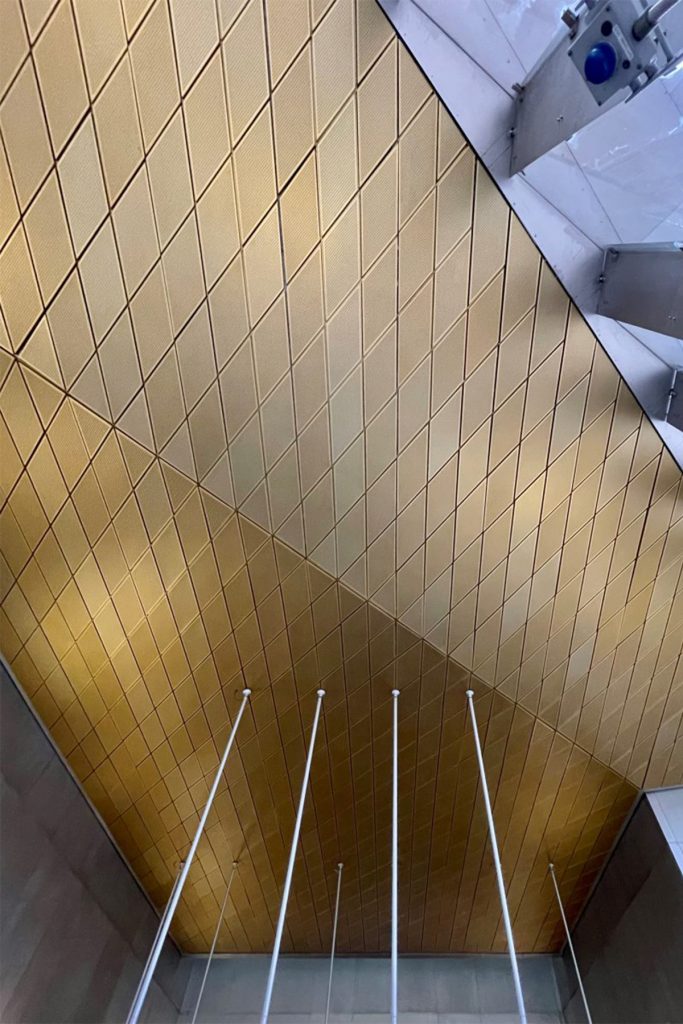
Showing the gold, or brass-coloured, anodised aluminium diagonally-set ceiling panels to the Wood Lane Underground Station, London. Architectural design by Ian Ritchie Architects. Ceiling by John Desmond Ltd.
Although aluminium is lighter in weight, the core material and the anodising process all cheaper than stainless steel there are sustainability considerations. The waste products from anodising are degraded sulphuric acid and aluminium hydroxide which require specialist removal and disposal. There are strict regulations controlling its disposal as if it is allowed to disperse in waterways it causes drastic and fatal damage to aquatic plants and animals and any adjacent wildlife. The relatively high cost of the specialist waste disposal means that this offsets the cheapness of aluminium as a material.
With regard to the aesthetic of anodised aluminium, although the colour is brass-like it is not quite the colour of brass or gold but a slightly mustardy tone and without the sheeny lustre of brass or stainless steel.
Brass and PVD Brass for taps, shower screens, bathroom fittings and accessories
Unlike the use of brass in the 1980s where it was mostly used on items in a traditional style, brass is today being used on contemporary fittings. The early nineteenth century taps below left are very familiar to us being in the “knobbly” style of tap with white ceramic indices for hot or cold. Today’s modern taps are cylindrical, minimalist and often brutal in their contemporary-ness yet designers are creating them in brass with no qualms or any sense of juxtaposition but as a natural extension of the tap design.
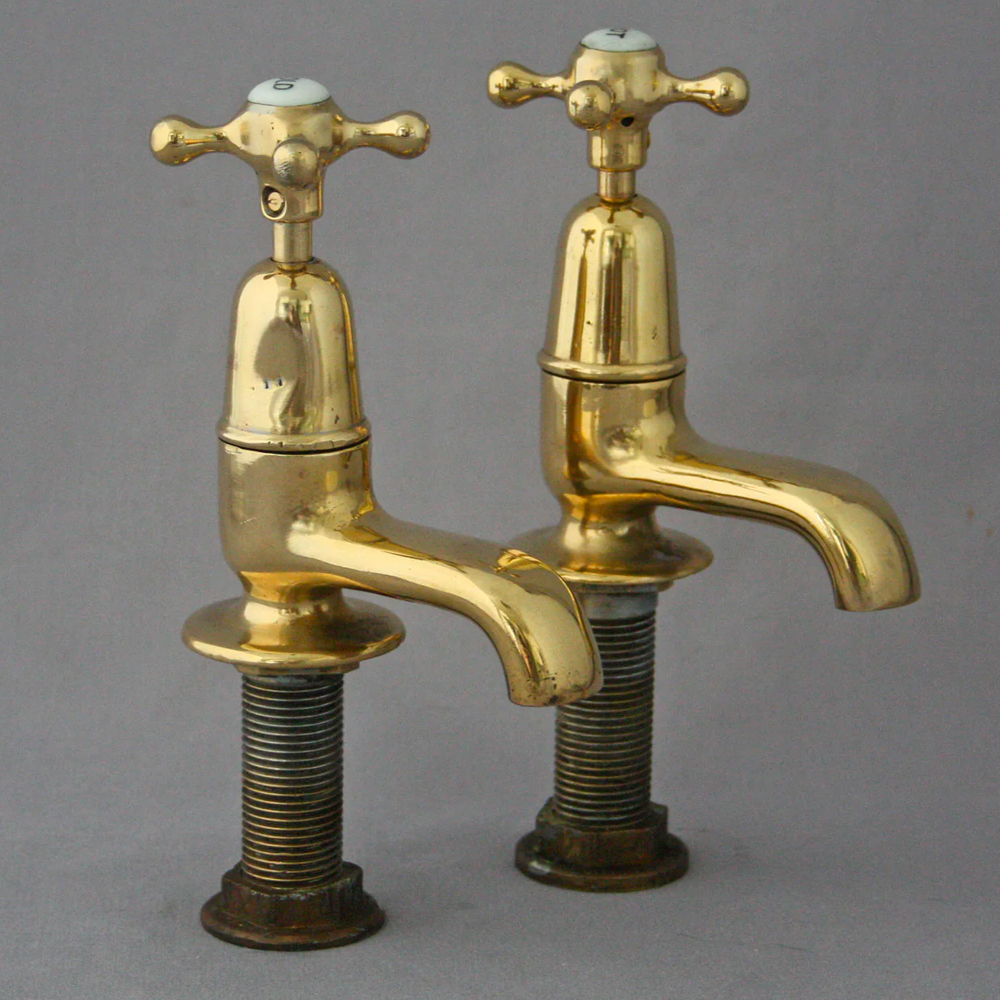
A pair of 1920s brass taps available from Architectural Decor based in Bristol, UK.
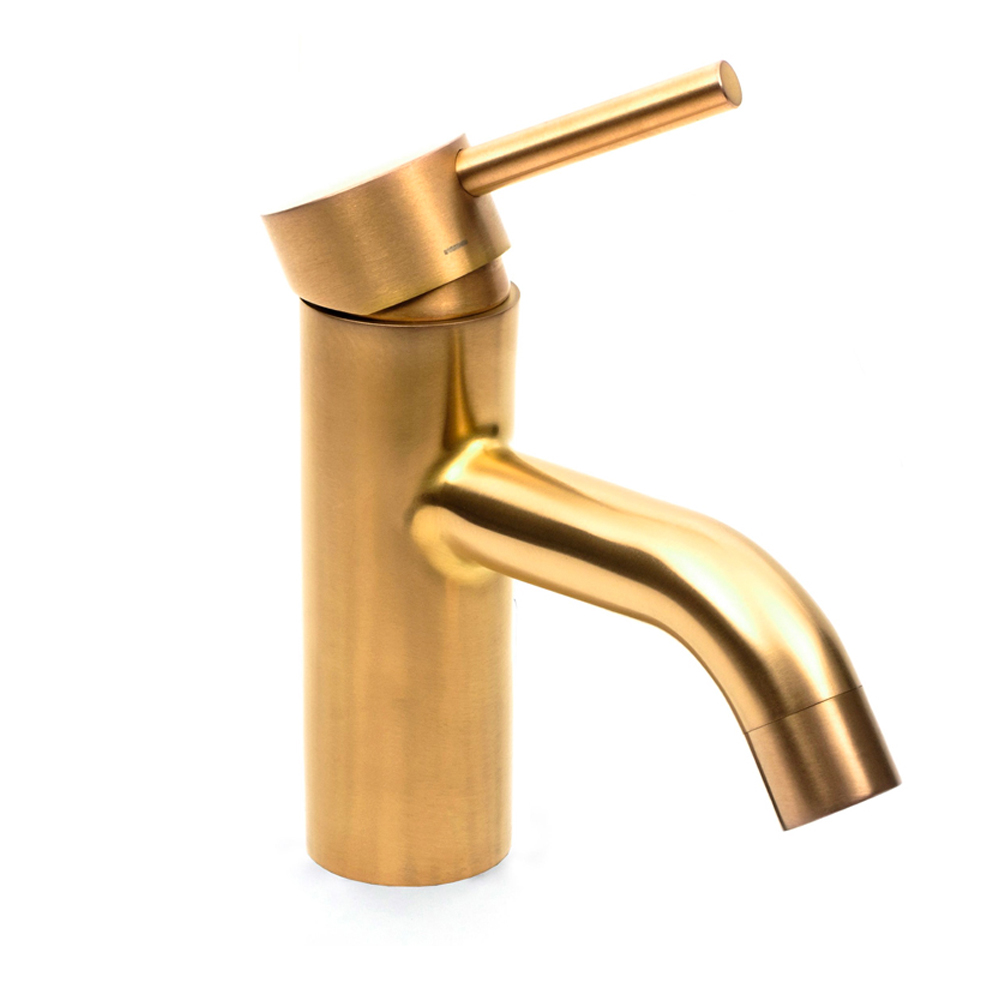
This contemporary tap by Dolphin Solutions is not brass but Brass PVD coloured stainless steel. The stainless steel used has a Brushed finish and you can see the surface of the tap has a soft, semi-matt sheen rather than a high shine as a result.
The benefits of producing taps in PVD coloured stainless steel rather than brass are that PVD does not tarnish or develop a green verdigris – which leads to pitting eventually, brass being relatively soft (60 on the Brinell hardness scale whilst stainless steel is between 180 and 400). Rather than being seen as a poor relation of brass PVD is being selected by sanitaryware designers as having both the high aesthetic needed and also the practicality of easy maintenance.
It is interesting to note that brass has started to follow in the footsteps of brass-coloured metals. As PVD for example is being used for innovative and contemporary bathroom design brass is now on offer performing the same functions. A good example is the brass-edged shower screen shown below.
Again, the fact that brass will discolour is not always a negative point as if it is kept maintained it does, of course, look beautiful and again the patina developed may indeed be even nicer. However if polishing a brass shower screen seems an onerous task then the PVD coloured stainless steel option might be preferable as this only needs a wipe over with a damp cloth and will not tarnish or pit.
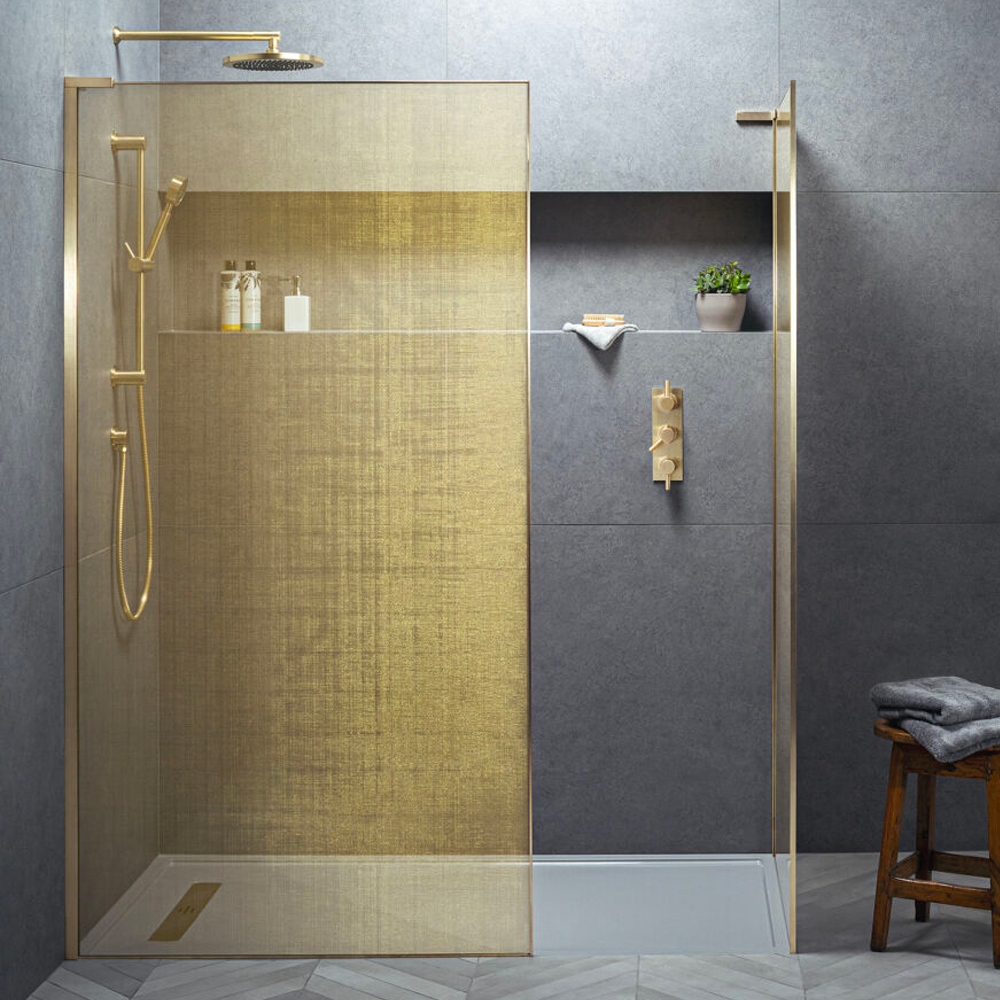
Shower screen edging in brass, available from Matki, also with the added detail of brass mesh integrated into the glass door.
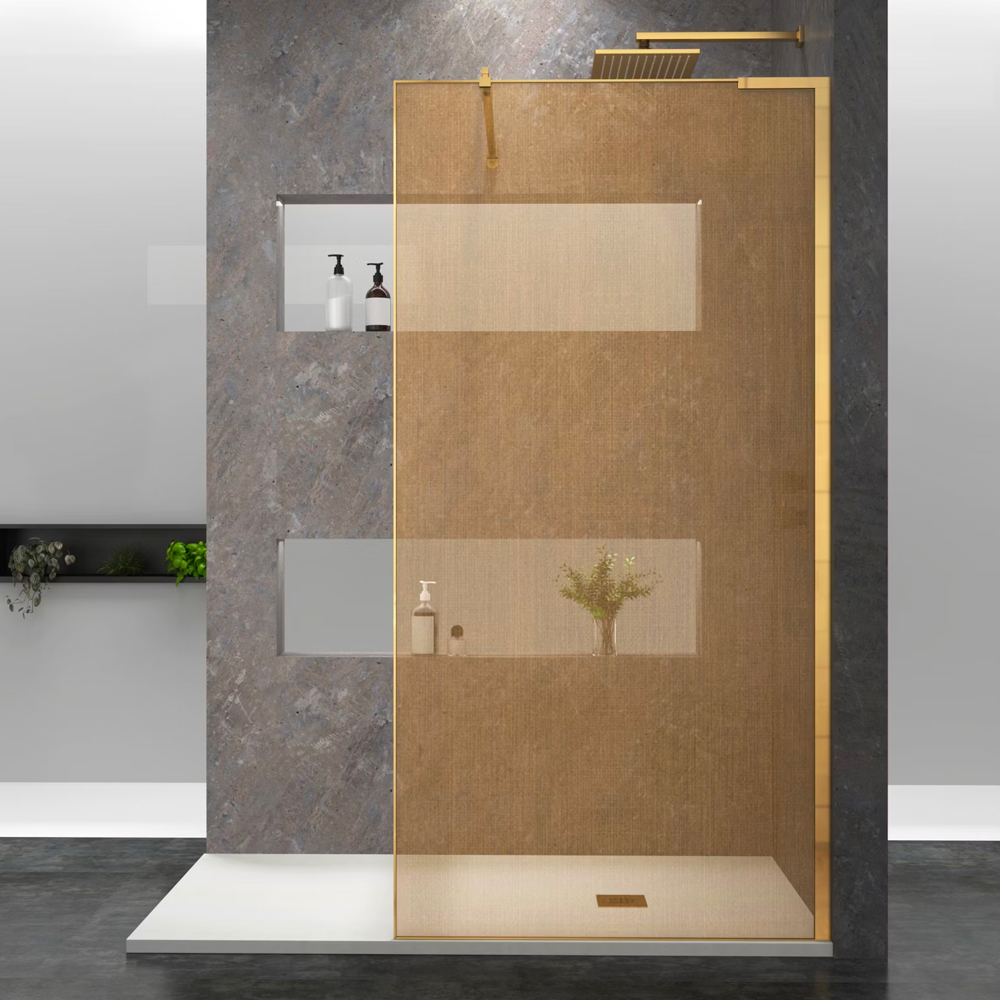
A very similar product, available from Royal Bathrooms, this time in PVD Brass Brush. Both will look beautiful – and unusual – in a bathroom however the PVD screen is a third to a quarter of the price of the solid brass and will not tarnish.
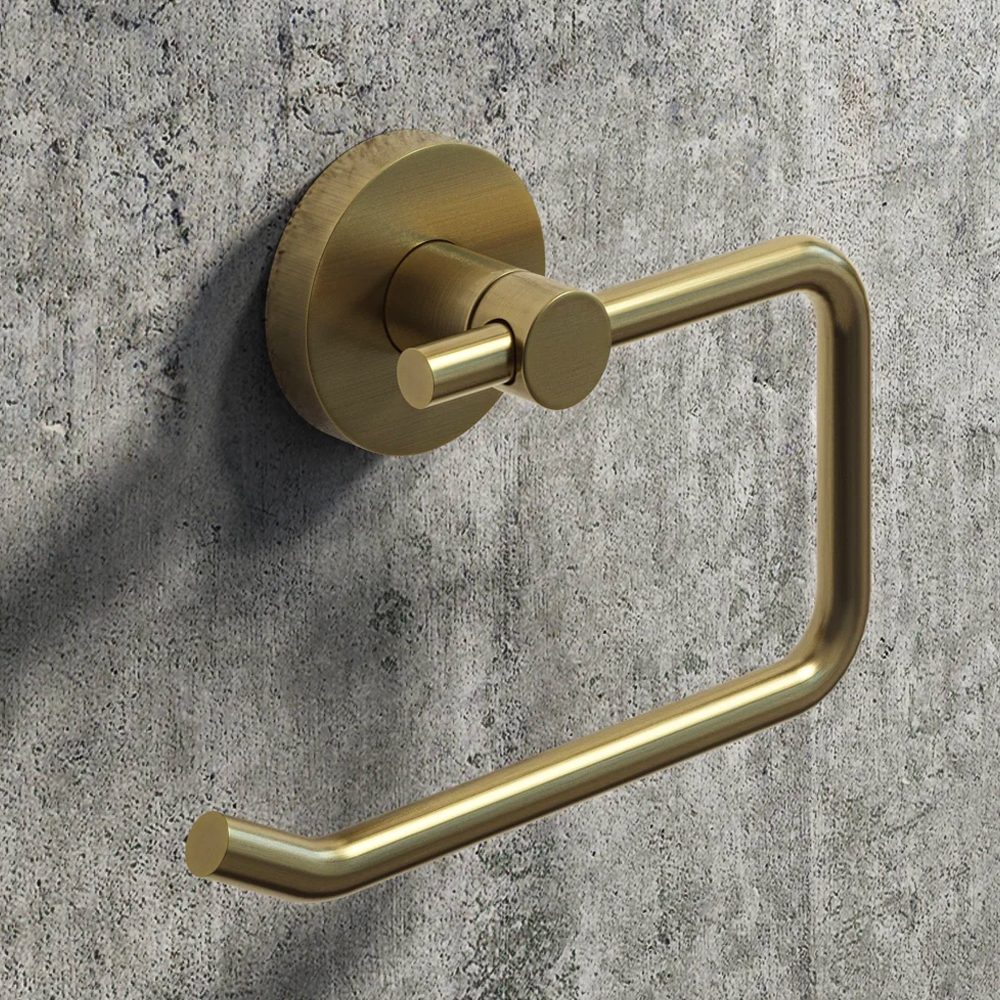
Brass toilet roll holder in brass by Arrezzo available from Victorian Plumbing.
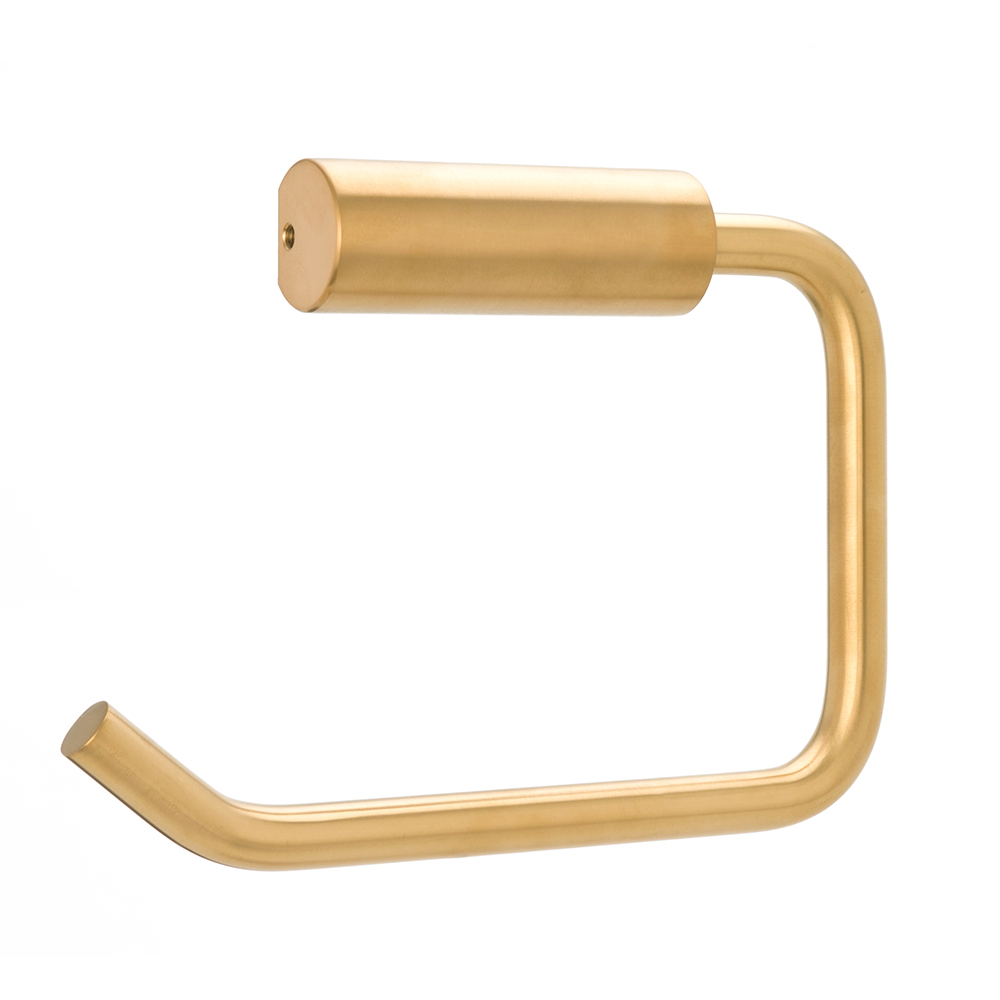
TDL.45 Single toilet roll holder in PVD coloured stainless steel in Brass Brush by The Splash Lab.
The same applies to bathroom fixtures such as toilet roll holders. Brass and Brass PVD coloured stainless steel are both used for traditionally-styled and contemporary fixtures.
PVD brass coloured stainless steel – enabling a matching suite of finishes across a collection of manufacturers’ products
PVD brass coloured stainless steel opens up the possibilities of having a suite of matching finishes across all items in a bathroom setting, for example:-
- Taps, shower heads and other plumbing fixtures
- Shower screen edging
- Grates and drains for wetrooms
- Mirror frames
- Lighting fixtures
- Cubicle doors, frames and panelling
- Towel rails and rings
- Paper towel dispensers
- Soap dispensers
- Soap dishes
- Toilet roll holders
- Toilet brush holders
- Grab bars
- Door furniture
- Kick and push plates
- Splashbacks
- Robe hooks
- Signage
- Socket and switch plates
- Architrave
- Tile-edging
- Door hinges
All of these items can be PVD-coloured to ensure a matching finish across a range of products and fixtures creating the look of a seamless interior despite the items being supplied by a variety of manufacturers. To obtain all these items in compatible designs with a matching brass finish would be very difficult, probably impossible. Selecting the products for their appropriate design, in their natural stainless steel form, and then processing them to be PVD coloured opens up a vast array of options to create a co-ordinating suite of fixtures. And, of course, PVD coloured stainless steel products can be matched to brass products so a mix of both can be specified with a visually harmonious result.
You can see in this washroom at Victoria Station, shown below, that the designers have used PVD to match the significant elements such as mirror framing, taps, countertop edging, cubicle doors, frames and partition. To do this in brass or copper would have been an expensive exercise as well as the cost of maintenance to ensure a patina did not develop. However fashionable it might be to have an aged look, in a public washroom it would not have been popular as it is important not only to maintain the highest level of cleanliness but also to look clean.
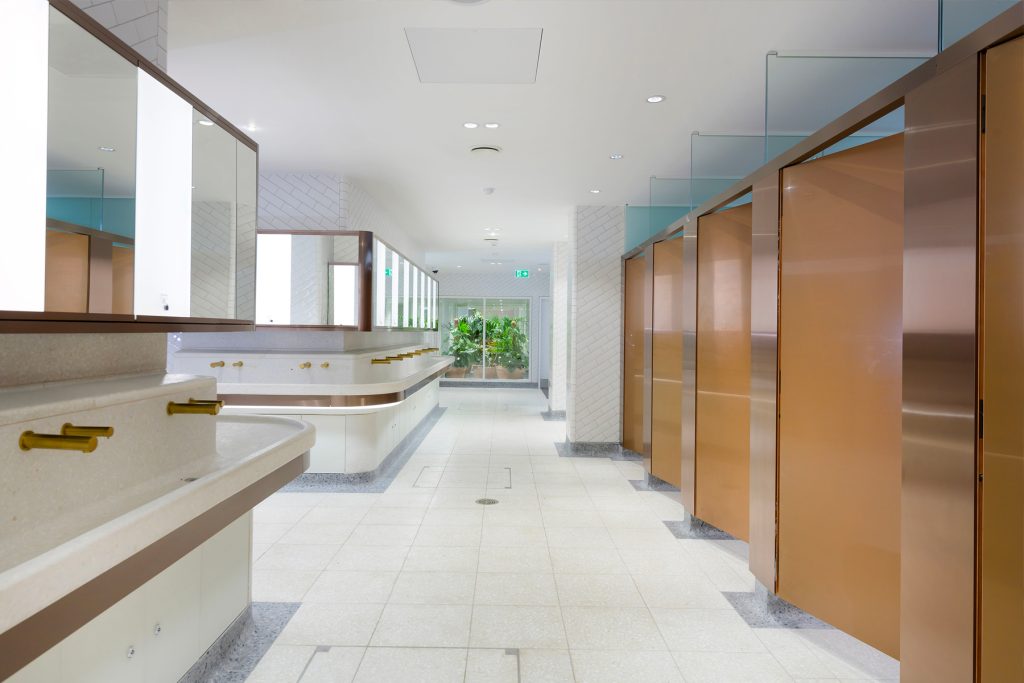
To conclude our exploration of applications for brass, PVD Brass and anodised aluminium…
Of course, brass will always be a favourite whether in its polished or aged state however the alternatives, such as PVD brass coloured stainless steel, offer real advantages. Weighing up which material to specify is never easy for architects and interior designers and, however desirable, specifying brass is frequently not viable for reasons of material and maintenance cost and practicality. PVD brass coloured stainless steel enables the breakthrough option of being able to fully capitalise on the delightful gleam of brass but without the drawbacks associated with the alloy itself.